中國網(wǎng)武漢5月28日訊中國高端制造技術(shù)又迎來新進(jìn)展。近日,華中科技大學(xué)張海鷗教授及團(tuán)隊(duì)采用自主研發(fā)的金屬3D打印“微鑄鍛”技術(shù),成功制造應(yīng)用于船舶重工等國之重器的大型泵噴推進(jìn)器槳葉,實(shí)現(xiàn)了復(fù)雜曲面構(gòu)件增等減材一體化復(fù)合快速制造,解決了3D打印技術(shù)中大尺寸零件制造中的“卡脖難題”。
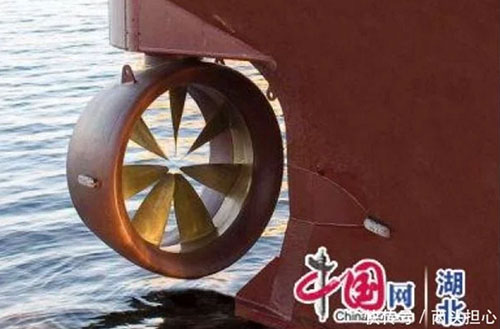
泵噴推進(jìn)器槳葉 資料圖
泵噴推進(jìn)器主要應(yīng)用于船舶重工等領(lǐng)域,是船舶航行的重要?jiǎng)恿ρb置。此次通過金屬3D打印“微鑄鍛”技術(shù)制造成功的大型泵噴推進(jìn)器槳葉,選用不銹鋼316L原材料,成型尺寸達(dá)到直徑0.6米、高度1米,總重量160千克。通過驗(yàn)收與測試,制造周期相比傳統(tǒng)方式縮短了2/3,構(gòu)件的力學(xué)性能得到了大幅度提升,制造精度差由以前的0.5mm提高到0.1mm,沒有檢測到鑄造缺陷如氣孔、裂紋等。
“常規(guī)金屬3D打印存在許多問題:一是沒有經(jīng)過鍛造,金屬抗疲勞性嚴(yán)重不足;二是制件性能不高,難免存在疏松、氣孔和未熔合等缺陷;三是大都采用激光、電子束為熱源,成本高昂。所以形成了中看不中用的尷尬局面!睆埡zt介紹,正因如此,全球金屬3D打印盡管在中小尺寸零部件制造中存在優(yōu)勢,但在大尺寸零件制造上無一法和大型鍛壓機(jī)相比,因此無法進(jìn)入大型復(fù)雜零件的高端應(yīng)用。
針對金屬3D打印這項(xiàng)世界性難題,張海鷗教授帶領(lǐng)研究團(tuán)隊(duì)經(jīng)過二十年努力,發(fā)明了“智能微鑄鍛”3D打印技術(shù),將金屬鑄造、鍛壓技術(shù)合二為一,實(shí)現(xiàn)了首超西方的邊鑄邊鍛的顛覆性原始創(chuàng)新。張海鷗介紹,金屬3D打印“微鑄鍛”不僅實(shí)現(xiàn)了綠色高效的短制造流程,還顯著提高了材料的疲勞壽命和可靠性,為船舶航行提供更為強(qiáng)勁、穩(wěn)定的“中國動(dòng)力”。
目前,相關(guān)產(chǎn)品已應(yīng)用于大型飛機(jī)、航空發(fā)動(dòng)機(jī)、燃?xì)廨啓C(jī)、航天、船舶、先進(jìn)軌道交通、核電等多個(gè)領(lǐng)域。業(yè)界普遍認(rèn)為,金屬3D打印“微鑄鍛”技術(shù)極有可能開辟機(jī)械制造史上前所未有的綠色制造新時(shí)代,助力中國從制造大國向制造強(qiáng)國轉(zhuǎn)變。 (王瀟瀟)